Top Warehouse and Industrial Racking Solutions: Revolutionizing Storage Efficiency
Whether it’s the business of logistics, manufacturing or supply chain management jobs, in today’s era everything needs to be done ahead of time in order to keep the lines of productivity and profitability open. Here’s an overview of the best warehouse and industrial racking solutions.
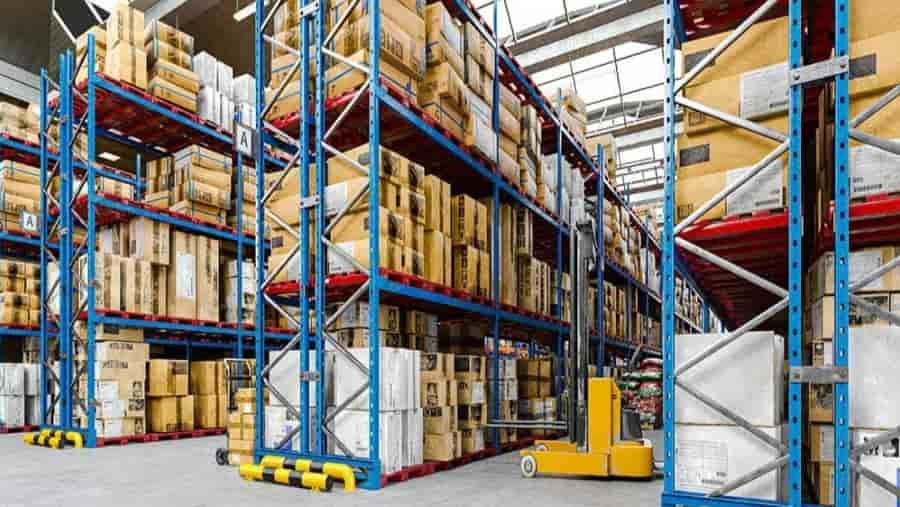
Everything you need to know about Racking Systems in Warehouses
Materials, whether raw or finished goods are predominantly storehouse in warehouses and industrial buildings. Traditional storage methods are often not very efficient, secure, scalable, etc. Racking systems provide for organized, effective, and overall cost-effective space storage solutions to meet these challenges. They aid firms optimize vertical and horizontal space, reduce operational overheads and enhance stock management.
Types of Racking Solutions
1. Selective Pallet Racking: Selective pallet racking is a easily used and versatile racking system. Allows easy access to every pallet, making it ideal for fast turnover warehouses. It is composed by racks, vertical frames and horizontal beams that combine to form storage bays. The selective racking is a flexible method of operation that suits various types of forklifts.
2. Bypass Storage Drive in and Drive Through Racking: For situations that require high density but do not rely on stock rotation, bypass storage drive in and drive through racking systems are more effective. Drive-in racking has forklifts entering at one end, and drive-thru racking allows pickup at both ends. It is best for large quantities of the same item, as they don't take up so much aisle space that you need to worry about dead spaces.
3. Push-Back Racking: A high-density style of racking system that uses a LIFO (Last In First Out) filing system. Here, pallets are stored across a rail system that enables them to be pushed back as new pallets are introduced. It reduces the need for unnecessary aisle space, thereby focusing on storage while still being very accessible.
4. Cantilever Racking: Cantilever racking is designed for the storage of long, bulky goods like pipes, lumber, and furniture. Its design has a freestanding support frame carrying the load horizontally, on arms. Cantilever rack can be customized for both length and height, making it a great storage system for businesses that have irregularly shaped or oversized stock.
Factors to Consider for Racking Solutions Selection
1. Storage Requirements: This will help you determine what kind of racking system is most appropriate based on the type and volume of goods that you store, as your storage needs will differ. A long-picked shelf balances product turnover, but high-density uses drive-in or push-back racking.
2. Space Availability: The available space per floor and height will dictate what type of racking system you can implement. For example, in warehouses with high ceilings mezzanine can be used.
3. Operational Needs: Consider how often inventory will need to be retrieved and what types of machines (e.g., forklifts) should be accommodated. High turnover better results obtain from selective pruning while less volume systems fit to high density systems.
4. Safety and Compliance: Safety is the major element of warehouse operation. Proper racking systems must adhere to guidelines and other industry-related standards to protect workers and keep stored goods safe.
In conclusion, leading warehouse and industrial racking solutions are one of those business assets in a hope that you love reading this, who help businesses improve their storage operations, enhance safety and remain competitive in a fast moving environment. Selective pallet rack’s rack for example, racking framework, between units, racks, conveyor lines, etc. By taking storage requirements, space constraints and operational needs into account, a company can select an optimal type of racking solution to increase efficiency and allow for expansion.
Guess you like
-
Tools to Ensure Data Security and How to Do: Safeguarding Your Digital Assets
-
Top Commercial Coffee Machines for Your Business
-
Investigating Philippines Discounted Luxury Container Homes and Trends in 2024
-
Most Useful SEO Ranking Tools in 2024
-
Work, Life & Online Marketing Degree
-
Vinyl Flooring: The Smart Choice for Every Family