Increase Production Output through Semi-Automatic Stretch Wrappers
As the focus is drawn to the global logistics and packaging industry, the key word for success is obviously speed. Semi-automatic stretch wrappers are a good balance of speed, cost and reliability necessary for firms that apply stretch wraps for unitizing products for shipment.
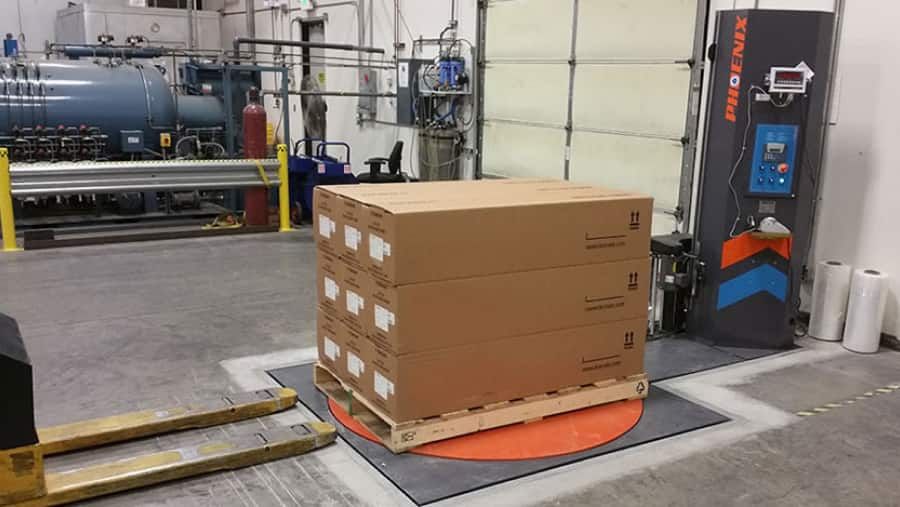
What Does Semi-Automatic Stretch Wrapper Actually Mean?
Semi-automatic stretch wrappers are equipment designed for the task of wrapping palletized loads with stretch wrap. In contrast to traditional hand wrapping, these machines help the operator in most of the wrapping process. The operator places the load on the turntable—or, in some models, positions the film—and the machine takes over from there, wrapping the load. This hybrid of partial automation strikes the perfect balance between manual labor and fully automatic machines and is thus a perfect choice for small to mid-sized businesses.
The semi-automatic stretch wrapper ensures consistent film tension and uniform wrapping, reducing operator fatigue. They are usually made in two different configurations, including a turntable wrapper, which rotates the pallet on a platform, and a rotary arm wrapper, where the arm glides around a stationary load. These design elements assure maximum stability of the load during transit, minimizing waste of film.
Benefits of Employing Semi-Automatic Stretch Wrappers
Investing in semi-automatic stretch wrappers has brought the following benefits:
1. Cost Savings: These machines reduce film consumption by as much as 55% due to their advanced pre-stretch. This is because the film is stretched before application, enabling a business to use less material with increased load security.
2. Higher Throughputs: Semi-automatic wrappers wrap 10 to 100 pallets daily, depending on the model and operational requirements. This ability enables companies to prepare more shipments in relatively less time than manual wrapping can provide.
3. Reduction of Labor Costs: Wrapping automatically by a semi-automatic machine enables the company to utilize labor in other more resourceful tasks. The effect of this efficiency can help reduce overall labor costs without loss of productivity.
4. Enhanced Load Stability: The consistency of wrapping ensures that pallets are wrapped tightly each and every time, reducing the likelihood of product damage in transit. This reliable method means better customer satisfaction because products arrive intact.
5. Improved Safety: Awareness of decreased reliance on repetitive labor, which may lead to strain and over exertion and probable work injury.
Best Semi-Automatic Stretch Wrappers of 2024
As we look into 2024, several semi-automatic stretch wrappers stand out due to their performance and features:
1. Robopac Masterplat: Capable of wrapping up to 30 loads per hour with advanced features like a self-learning wrap program. Price range: $10,000 - $15,000.
2. ITW Muller Raptor Plus: Offers turntable wrapping for up to 45 loads per hour. Known for its robust design and efficiency. Price range: $8,000 - $12,000.
3. Orion Flex Standard LP: Designed for versatility with both forklift and pallet jack loading options. Price range: $7,000 - $11,000.
4. Arpac Pro Series: A cost-effective option that includes full powered pre-stretch capabilities for improved productivity. Price range: $6,000 - $10,000.
The feature variations of these machines includes the capacity of the loadbearing, speed of the machines and adaptation to various pallet sizes and weights.
How to Choose Cost-Effective Semi-Automatic Stretch Wrappers
Selection of the right semi-automatic stretch wrapper requires great consideration of some key factors, including:
1. Analyze Your Requirements: Consider how many pallets you need to wrap in a day. For less than ten pallets a day, manual methods will suffice, while semi-automatic machines are highly essential for high-volume applications.
2. Inspect Features: Look for machines with pre-stretch capabilities, which will improve film usage without sacrificing load security. Other useful features include variable containment force, which can be helpful in handling various types of loads.
3. Plan Space: Make sure the facility has room for the machine’s footprint. Low-profile models are ideal for pallet jack operations, while high-profile models work better for forklift operations.
4. Budget Wisely: Though the costs vary widely at their inception, from $6,000 to over $15,000, long-term savings from reduced labor and material costs should be factored into your decision.
5. Seek Vendor Support: Select a manufacturer or supplier that has extended customer support and training services to make the after-sales operation smooth.
Guess you like
-
Everything You Need to Know About Palworld
-
Pourquoi Devrions-Nous Connaître les Femmes Âgées Célibataires à Proximité ?
-
How to Get a Jitterbug Phone for Free for Old People
-
Figure Out How to Get Free 5G Phone From Government
-
How Do Psychology Graduates Stand Out in the Job Market
-
A Comparison of Microsoft's Surface Book and Surface Pro Laptops